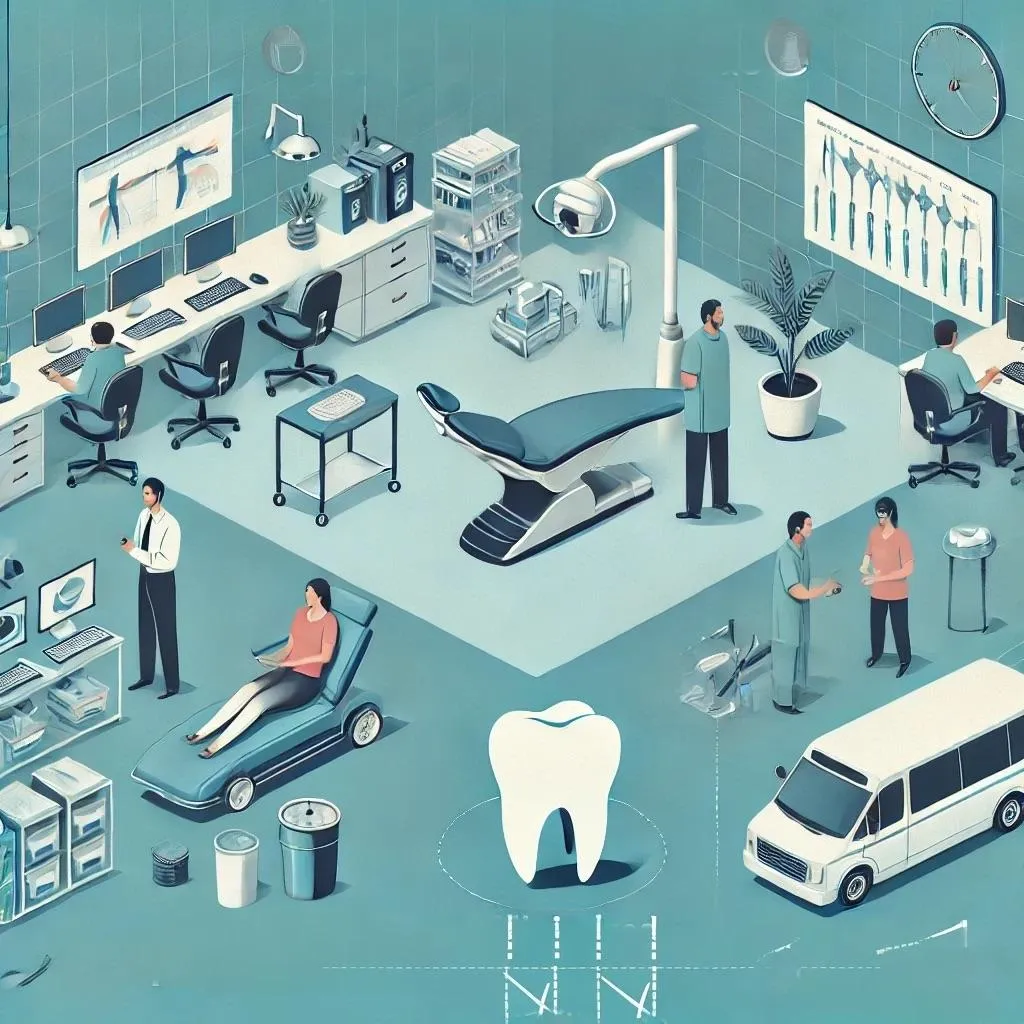
Understanding and Eliminating Transportation Waste from Your Dental practice
In the journey to streamline operations and improve efficiency, understanding and eliminating waste is crucial. One significant type of waste in the Lean management system is transportation waste. Let's dive into what transportation waste is, how it manifests in everyday settings, and how it can specifically impact dental practices. We'll also provide practical steps to identify and eliminate transportation waste in your practice.
What is Transportation Waste?
Transportation waste refers to the unnecessary movement of materials, products, or information. This type of waste does not add value to the end product or service and can lead to increased operational costs, longer process times, and reduced efficiency. In essence, any movement that does not directly contribute to the value of the service being provided is considered transportation waste.
Everyday Example: Transportation Waste in a Coffee Shop
Imagine a busy coffee shop where baristas have to walk back and forth between the coffee machines, storage areas, and the counter where customers place their orders. If the coffee beans are stored far from the coffee machines, every time a barista needs to refill the beans, they waste time walking to and from the storage area. This unnecessary movement does not add any value to the customer who is waiting for their coffee. Now there isn’t a single-right answer. All businesses are different; therefore, there are multiple answers to the problem, here is two examples:
If there were serious spacial constraints and the layout couldn’t be re-designed, the coffee shop could train operators to specialise in the role of ‘replenishments’. This role would then become critical in ensuring all baristas remain up and running all the time, maximising their time ‘adding value onto customers’.
If the coffee shop was less restricted, by redesigning the layout to place coffee beans closer to the coffee machines, the coffee shop can reduce transportation waste, speed up service, and improve overall efficiency.
Transportation Waste in a Dental Practice
In a dental practice, transportation waste can occur in various forms, leading to inefficiencies and increased operational costs. Here are some examples:
1. Movement of Patient Records:
Issue: Physical patient records, or imprints, scans, are stored in a central location, requiring staff to walk back and forth to retrieve and return them.
Impact: This unnecessary movement takes time and can delay patient care.
2. Transporting Dental Tools and Supplies:
Issue: Dental tools and supplies are stored in multiple locations, leading to frequent trips to gather necessary items for procedures. A common example is X-Rays machine being in a different room from the examination room - causing patients to walk back and forth.
Impact: This can lead to longer setup times and reduced productivity. It may not seem like long - but imagine 5-10 patients a week walking to/from the X-Ray machine.. now multiply that out to a whole year!
3. Patient Movement Between Rooms:
Issue: Patients are required to move between multiple rooms for different stages of their visit (e.g., from the waiting room to the consultation room to the treatment room).
Impact: This can cause delays and discomfort for patients, reducing overall satisfaction.
4. Staff Movement for Administrative Tasks:
Issue: Administrative tasks, such as filing paperwork or processing payments, require staff to move between different areas of the practice. A common example here is enquiries being received by phone, receptionist writing it down on paper & then transposing the information onto a system.
Impact: This can lead to wasted time and reduced efficiency.
5. Delivery of Lab Work:
Issue: Dental impressions and lab work is needed for a patient to be called back in. Practices are having to constantly chase labs for an update. The chasing work, emails, phone calls & updates sent to patients is a form of transportation waste.
Impact: This adds time to the overall treatment process and can delay patient care.
Getting Started with Observing, Quantifying, and Removing Transportation Waste
This is all well and good in principle. But what if you are running a practice, doing clinical work, and managing your staff? How do you get time & the experience to do the improvement work? I hear you.
For those with little background in Lean principles, here are some practical steps to start identifying and eliminating transportation waste in your dental practice:
1. Observe and Document:
Action: Spend time observing daily operations in your practice. Take notes on the movements of staff, patients, and materials.
Tip: Use a simple checklist to track unnecessary movements and identify patterns.
2. Map the Process:
Action: Create a process map that outlines the flow of activities in your practice, from patient check-in to treatment and checkout. Alternatively, do a little sketch of your practice layout, and draw lines indicating the movement of people/information/staff members - those are known as Spaghetti Diagrams. Thick branches indicate opportunities.
Tip: Highlight areas where excessive movement occurs and consider ways to streamline these processes.
3. Engage the Team:
Action: Involve your staff in identifying transportation waste. Encourage them to share their observations and suggestions for improvement. What’s their biggest pain points? Don’t forget - what you hear could be a symptom of something of a bigger problem.
Tip: Hold regular team meetings to discuss potential improvements and implement small changes incrementally. In the manufacturing & operations world those are called Gembas (keep your eyes open - I will write something about this). The idea of Gemba is to allow your staff members to present the key challenges they are facing so that you - as a management team - can fix it to make their jobs easier.
4. Quantify the Waste:
Action: Measure the time and distance involved in unnecessary movements. Use simple metrics such as steps taken, time spent walking, or the number of trips made.
Tip: Use these measurements to set benchmarks and track improvements over time.
5. Implement Changes and Monitor:
Action: Make changes to reduce transportation waste, such as reorganizing storage areas, digitizing patient records, or redesigning patient flow. This is typically known as 5s’ing. It’s essentially ensuring that everything is in order and has a home. If all tools and stock have a home, it is easier to find them reducing time spent.
Tip: Monitor the impact of these changes and continue to refine processes based on feedback and results.
Final Thoughts
Eliminating transportation waste is a vital step in improving the efficiency and effectiveness of your dental practice. By understanding what transportation waste is, recognizing how it impacts your operations, and taking practical steps to reduce it, you can enhance patient care, increase productivity, and reduce costs. Embracing Lean principles and continuously seeking ways to minimize waste will help keep your practice competitive and responsive to the needs of your patients.